Background of "Smart Factory" in injection molding factories
There is an increasing need of effort for incorporating smart technology induced by various social challenges like Industrial 4.0 advocated in Germany, IoT proposed by General Electronics as a representative industrial internet, a decrease in the working-age population, and a lack of human resource due to aging population.
7 key points for "Smart Factory" initiatives
"Smart Factory" roadmap survey
According to the Japanese Ministry of Economy, "Trade and Industry's Smart Roadmap Survey", the following 7 items are the key points for smart factory.
- Quality improvement
- Cost reduction
- Improve productivity
- Reduction of time to commercialization and mass production
- Responding to human resource shortages and training
- Provide new added value
- Strengthen risk management
"Total Link" will support to solve the 7 key points happening at injection molding factories
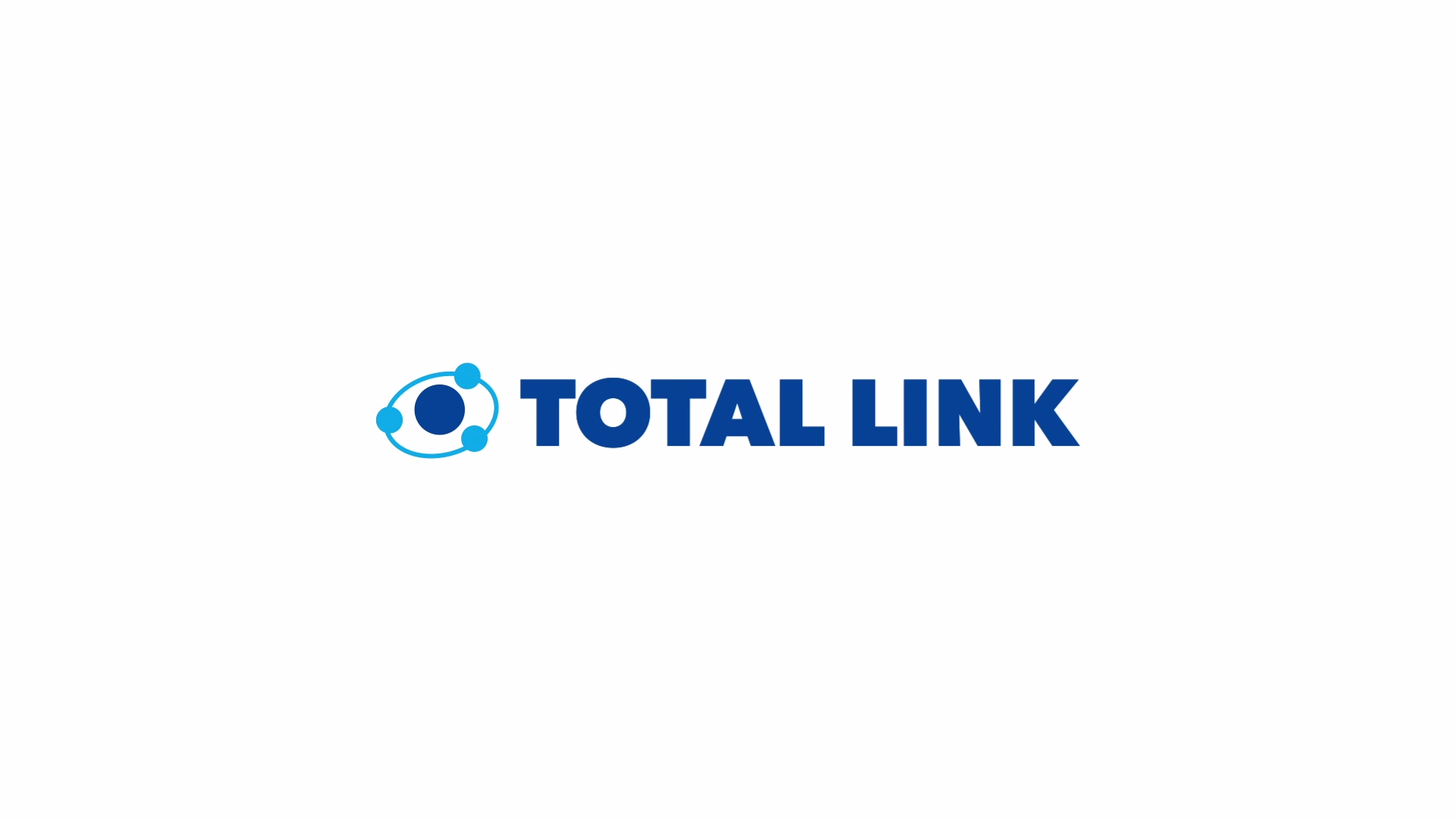
Quality improvement : Take-out robot monitors peripheral devices
In the following cases, defective products would be occured in injection molding factories.
- Shut down by a thunderbolt struck
- Change in mold temperature due to a clogged pipe of temperature controlling machine
- Change in resin drying temperature due to poor quality of peripheral heating equipment
To solve such problems, a take-out robot that can monitor peripheral equipment would be helpful. Once connected with peripheral equipment, it alarms abnormal activities of the surrounding in the molding process.
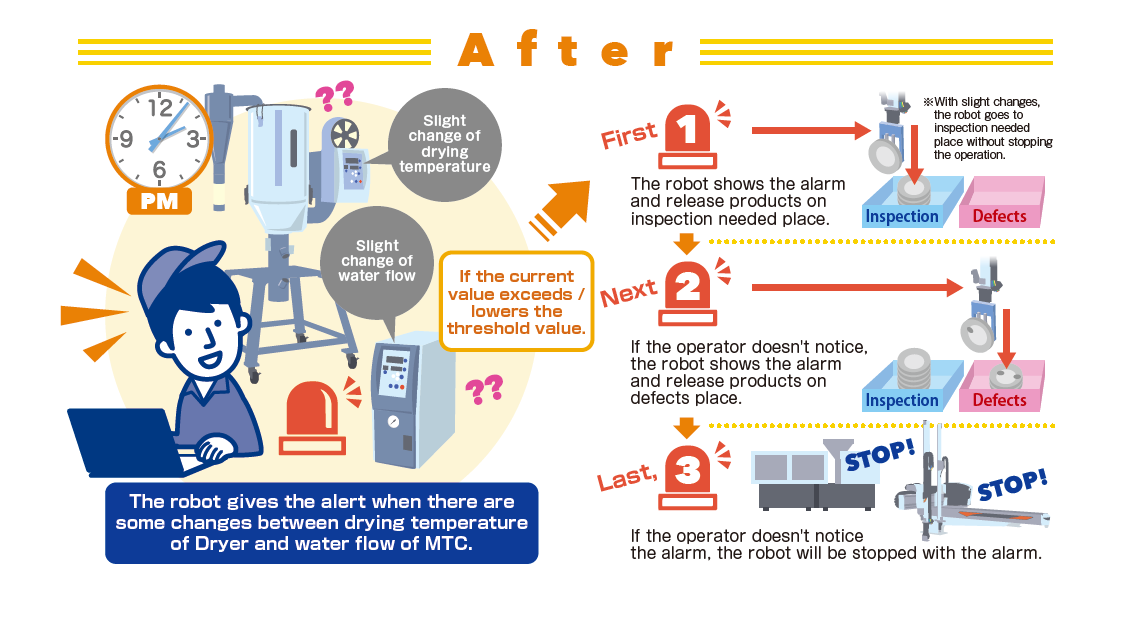
With Total Link, the quality improvement of molded products can be expected through an attempt to decrease the chance of producing defects which are likely to happen when they are not carefully watched.
Central management of peripheral equipment : Setting, Activation, and Termination
The human errors in setting and activation will be improved with the central management. It controls the take-out robot and all the peripheral equipment and unifies the setting, activation, and termination.
Cost Reduction : Reduce the material cost by removing excessive material purge
The excessive materials left in the hopper dryer after molding are usually thrown away or manually removed by human. With Total Link, it is possible to serve the minimum usage amount of resin to the hopper dryer so that there will be no excessive materials left.
When the production quantity is registered in advance with the robot controller, the take-out robot automatically calculates the optimum material transportation time at the end of molding based on the molding cycle of one shot and the time required for normal material supply. The robot supplies the minimum amount of resin material at the end of the molding cycle. This eliminates unnecessary material purging and reduces material costs.
Productivity improvement : Reduce the downtime of the molding equipment
If you face following problems, Total Link may help you.
- The equipment alerts and stops working but there was no quality problem
- It takes time to check the material purge and reactivate the molding equipment
Total Link allows the robot controller to set threshold values for monitoring temperature and flow abnormalities of each peripheral equipment in advance. The robot controller communicates with each peripheral equipment, and if the threshold value of each peripheral equipment is exceeded during automatic molding operation, the robot automatically sorts out products that may be defective.
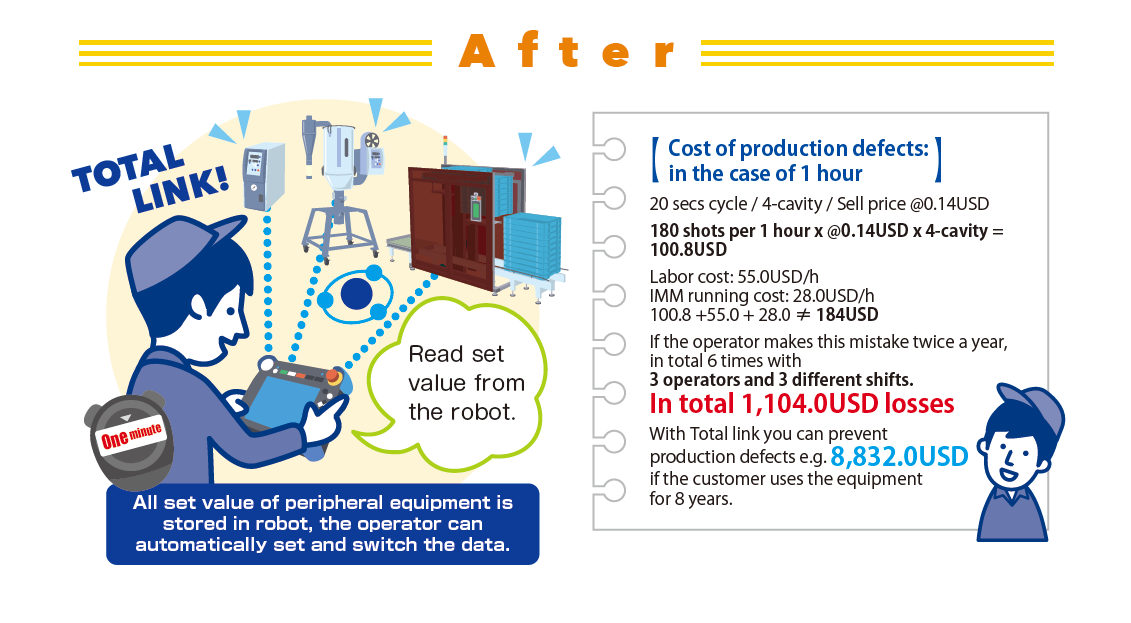
In addition, based on information from each peripheral equipment, an alarm is issued to notify the user of any abnormality if a threshold value is exceeded. This function allows the system to notify quality errors and peripheral equipment errors while maintaining continuous production of the molding machine, thereby contributing to improved productivity by reducing molding machine downtime.
Improvement in Labor shortage and Training
Since the setup of each peripheral equipments (e.g., settings, activation, and termination) varies, the workers need to take care of them for several times.
Total Link allows the robot controller to memorize the temperature settings and startup times of peripheral equipment for each mold in advance, allowing for integrated management of peripheral equipment settings, activation, and termination.
This system will the amount of setup work per worker due to labor shortages. It can also address labor shortages and training issues by automating tasks that were dependent on specific workers.
Risk Reduction : Traceability of defective products
There are many factors causing defects such as materials, mold , injection machine and peripheral equipment. Therefore, it is necessary to take time to specify the cause.
Total Link can memorize data on the operating status of each peripheral equipment obtained through robot controller and peripheral equipment communication. In the unlikely event of a defective product leakage, the data can be traced to see if the problem is caused by an abnormality in a peripheral equipment. Time and labor for identifying the cause can be reduced.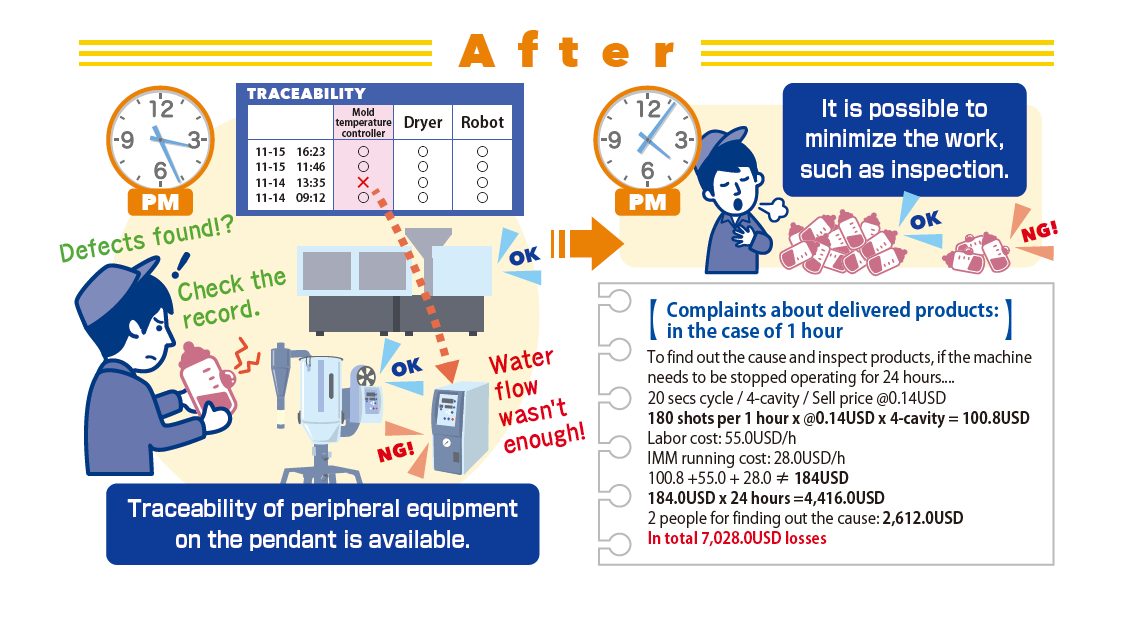
The traceability of Total Link helps reduce the time and cost to specify the cause of defects, improving the risk management.
Total link with molding machine peripherals and data
The controller of the take-out robot has the same digital capabilities as a PC. Taking advantage of this characteristic, Harmo's Total Link connects with peripheral devices and collects data.
Based on this data, the robot can make its own decisions to change its behavior and monitor and control the movements of peripheral devices. That is Total Link.
It contributes to the creation of smart factories.
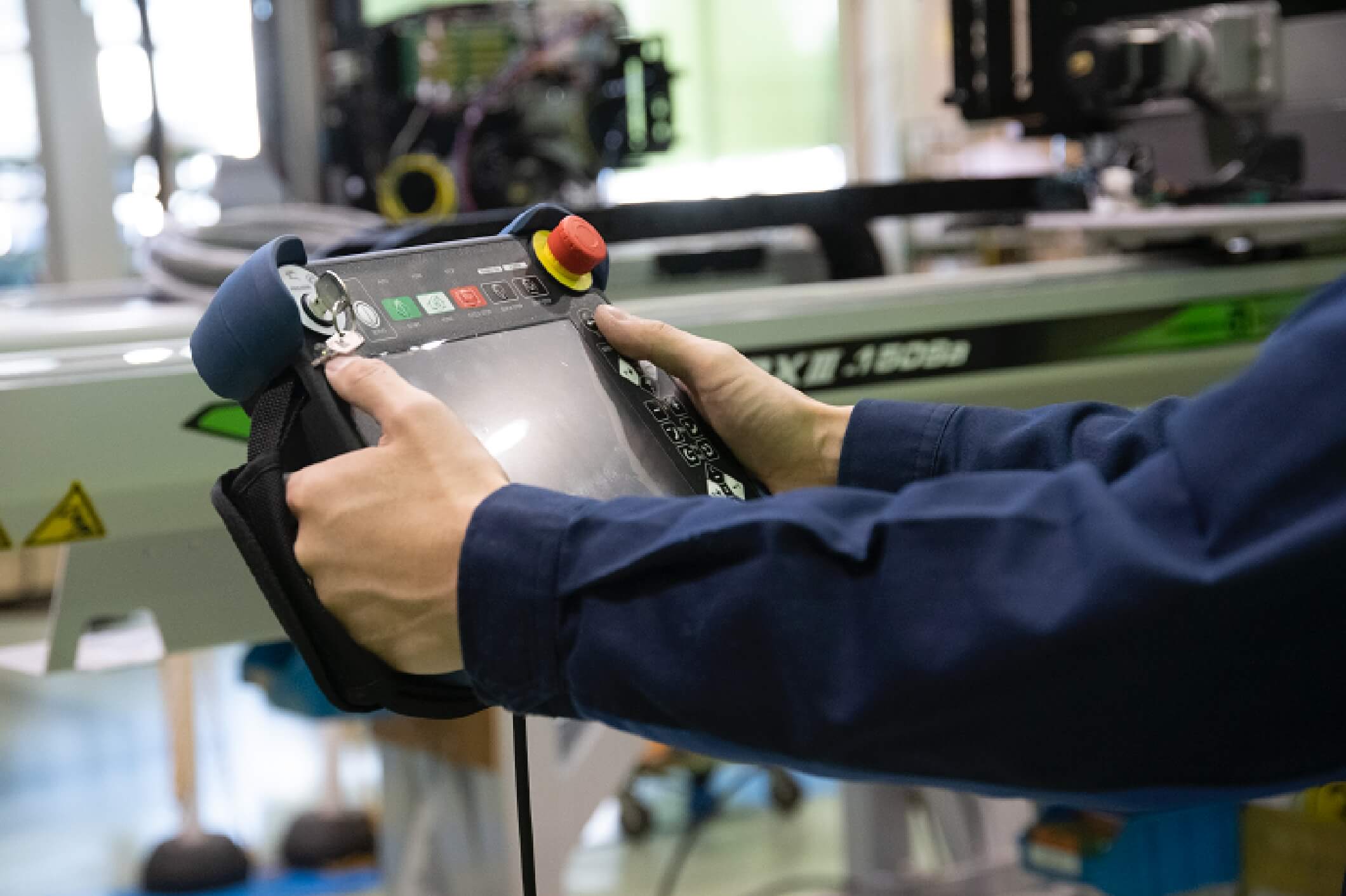
Download the document
Harmo's total link contributes to the smart factory.
Recommend for
- Injection molding setup is labor intensive (injection molding machine operator)
- Difficult to notice when equipment is out of order (production line manager)
- Traceability of molded products cannot be ensured (quality controller)
- Livelihood cost shade depends on workers' skills (factory manager)
- Headache due to lack of manpower on site (manager)

Please find below to watch the video