Currently, the process that requires the largest number of operators at the molding site is the post-processing of the molded product.
For example
For example, 15-second cycle molding, 4 cavities
- 4 cavities per 15 seconds
- 20 cavities per 75 seconds
Operators have to do boxing work such as carton box to transport them to the next process, and as a result, one person becomes a person in charge of one molding machine.
Concerns / Tasks
- 100 machine means they need 100 operators
- For 3-shift and 24 hours operation, about 300 operators are needed
- High labor costs for night shifts
- Counting mistakes caused by human error
- Defective products caused by dust and foreign matter due to the use of operators
- There is not enough time to take care of one more machine, even though there is time for a hand to rest when boxing a 4-cavity every 15 seconds
Solution & Advantages of using box filling system
Solution
Change from conveyors to container type box filling system.
Advantages
- Unattended operation for long periods of time without restriction if space is available.
- Reduces labor costs by allowing one person to manage multiple machines instead of one person managing one machine.
- No damage to the products as they are stored in boxes by highly accurate take-out robots.
- When a container is full, the next container is used to cover it, reducing the possibility of dust and foreign matter being mixed in during transportation.
- There is no need to purchase new containers as the current ones can be used as they are.
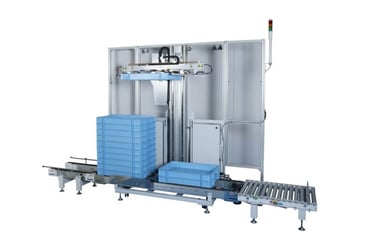
Please find below to watch the product introduction movie
Download document
Contents
- 5 check points to decide whether or not to install box filling system
- Let's see how much the payback is.
- Example and reputation from the customers
- The reason why the customer chooses Harmo's box filling system (features of ST series and demonstration)
- Q&A
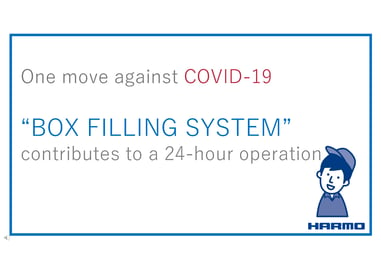
